It’s always important to understand the value of proper machine maintenance and investigate ways to help you get the most out of your equipment. After all, if you don’t take care of your machinery, it won’t run as smoothly, reliably and efficiently as it could and won’t last as long as it should. The bottom line is that there is no replacement for proper maintenance.
In this guide, learn more about your Toro® products’ oil, grease and engine lubricant best practices to keep your equipment running right for years of efficient and effective use.
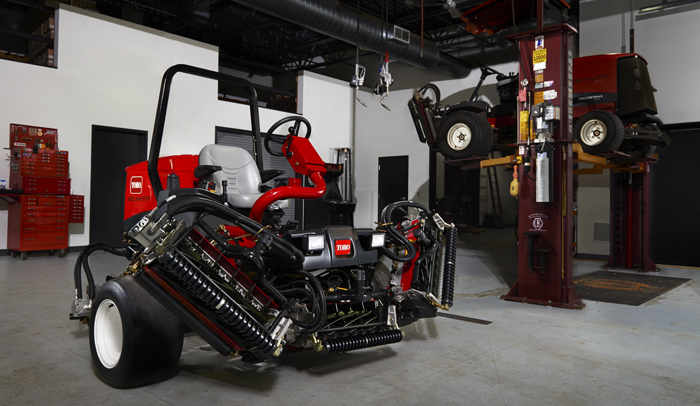
Choosing the right grease and oil
The purpose of grease is to stay in contact with and lubricate moving parts without seeping out under the effects of gravity, centrifugal force or getting squeezed out under pressure. It needs to retain its properties under shear forces at all temperatures it encounters during use. Different applications require different grease viscosities for peak performance.
Grease is extremely important for any machine, but choosing the right grease for your application is not always easy. Refer to your equipment’s owner’s manual for your best option. The grease that is indicated in most Toro manuals is typically a NLGI #2 lithium grease (commonly referred to as No. 2 lithium grease), and Toro usually states specifications for all oils and lubricants so customers can easily source them.
As far as engine oils, engine manufacturers specify their oil type and grade for the product itself, and it’s typically found in the machine’s operator’s manual as well. It’s also more officially called out in the engine owner’s manual or service manual that customers should have access to.
There should be a maintenance decal on the machine and operator’s manual for the type of oil and grease points. The example below is from a Model #44549 ProForce® Debris Blower operator’s manual; other machines have similar decals.
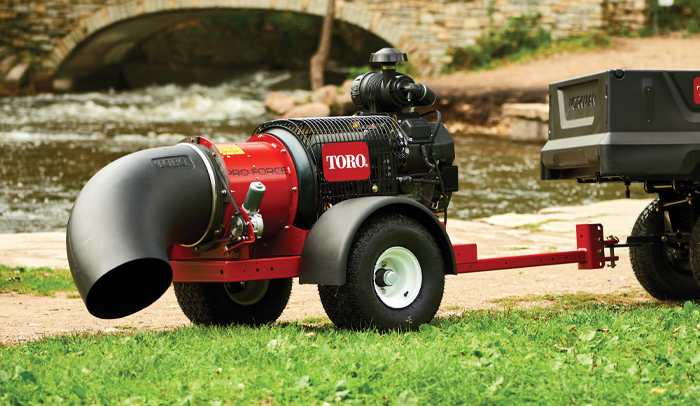
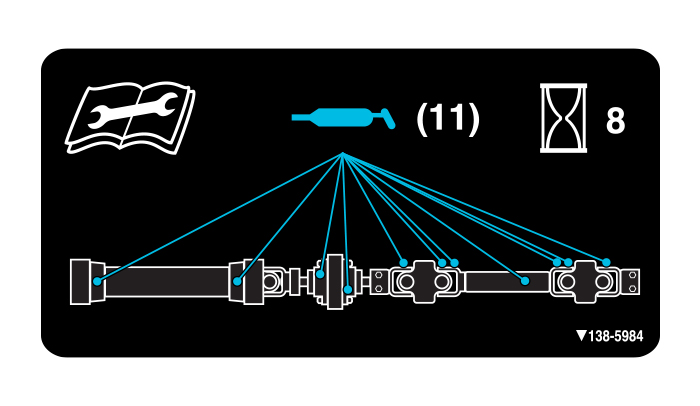
Don’t forget about attachments and accessories
From groomer boxes to gearboxes to PTO shafts and more, you likely have accessories and attachments that may or may not be permanently attached to your equipment. They may be detached and stored off to the side somewhere. So, when doing any sort of maintenance on your machines, whether it’s routine scheduled maintenance or seasonal upkeep, you need to remember the other accessories and attachments stored in the back of the shed. They may need maintenance as well and require oil, grease and/or hydraulic fluid.
The importance of hydraulic fluid
Today’s hydraulic fluids serve several purposes. The main function of a hydraulic fluid is to provide energy transmission through the system, which enables motion. Hydraulic fluids are also responsible for lubrication, heat transfer and contamination control.
In an effort to provide customers with value-added improvements, Toro has changed its standard-fill hydraulic fluid from Toro Premium All Season Hydraulic Fluid to an extended-life hydraulic fluid — Toro PX Extended Life Hydraulic Fluid.
The new Toro PX Extended Life Hydraulic Fluid allows for increased hydraulic fluid and filter change intervals, eliminates the initial low-hour hydraulic fluid change, allows for common change intervals across product offerings, which reduces confusion during maintenance servicing, and lessens the overall cost of ownership.
For more information and to see which Toro products are affected by this change, see our Service Bulletin. Please note that not all machines use Toro PX Extended Life Hydraulic Fluid as some require tractor transmission fluid. The Toro commercial products GM7210, GM360 and Outcross will continue to use Tractor Hydraulic Fluid as it is supplied currently. No changes will be made to the Tractor Hydraulic Fluid product.
Dealing with degradation
Whether it’s new or not, hydraulic oil and engine oil that sits for a while gets old and degrades, so these fluids must still be replaced. Grease is no different. Due to heat, moisture or the passage of time, degradation of oil and grease leads to the breakdown of additives, which in turn leads to increased acidity, oxidation, varnish and thickening. Those are issues you don’t want in your oil and grease because they essentially react with the metal and lose their effectivity, and it can simply cause harm just by sitting in there due to corrosive properties.
When severe degradation exists, such as in poorly stored equipment or equipment that has been stored long-term, it should be treated like excessive contamination.
Contending with contaminants
Contaminants such as dirt, engine blowby and moisture after washing can be normal. Extreme contamination would be issues like excessive moisture from complete submersion of a component, excessive blowby from a poorly running engine and metal contamination, which might be an indication of a larger concern such as a damaged component that will require further investigation.
Note that hydraulic systems have limited ability to remove moisture from the hydraulic fluid, making it important to not directly spray the breather of the hydraulic reservoir with water when washing the machine to ensure moisture is not introduced into the system. Should excessive moisture be found in the hydraulic system, the hydraulic fluid will need to be changed to prevent component damage.
Replacing oil and grease
Normal degradation or contamination can be handled during routine maintenance when fluids and filters are replaced and regular greasing occurs. If equipment has not been properly maintained, has gone too far past routine maintenance and has been neglected, debris can fall out of suspension and cause problems. If excessive debris is found, a purge or full cleaning of the old grease or a system flush of the old oil would be the next level of maintenance.
For greased components, you might be able to pump in enough grease to push out all the old grease. With a bearing, for instance, you want to ensure you’re pumping in good, clean grease and the bad grease is coming out. But if the component being serviced is not built to accommodate this method, disassembly and cleaning with a solvent would be required.
For an oiled system or component, multiple drain-and-fills and the use of an inline filtering system might be required to properly remove contaminants.
Be sure to note that in all cases where excessive debris is found, if the debris is from a damaged or failing component, something needs to be repaired or replaced. No amount of new grease or oil will resolve issues stemming from damaged or failing components.
On the other hand, there are many greased components that do not have grease fittings. There are certain bearings that are sealed and don’t need grease, and there are suspension parts that are not greased due to the material acting as a self-lubricating component.
Keep machines running reliably with proper maintenance
Without a doubt, performing regular maintenance on your equipment will extend its life and help it work its best all season long, year after year. If you have questions about these practices, contact your local Toro distributor for more information.
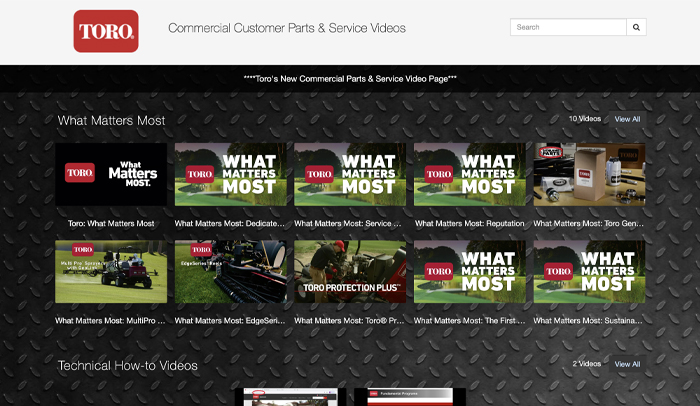
More how-to help
The how-to series is designed to help you get the most from your Toro equipment. If you missed any of the previous articles, just click on the titles below. You can also check out our Video Hub for more how-to instructions and advice.
Reduce Costs with Hybrid Technology
Extending the Life of Your Sprayer
Maintaining the Ideal Quality of Cut
Extending Equipment Life with a Fuel Stabilizer
How to Choose a Rotary Blade or Bedknife
Tier 4 Regeneration
Hose Maintenance
Use Service Reminders to Ensure Timely Maintenance